Ultrasonic flowmeters (USMs) have been commercially available since the 1960’s and have achieved widespread adoption in a range of process applications. However, USMs are not perfect as there are a variety of common process conditions that can significantly affect their performance. This means that the advantages of USMs can only be reaped if care is taken to install and use the meter properly.
USMs come in a variety of different forms — utilizing various methods for measuring flow, such as the transit time principle and Doppler effect principle, which are described later in this article. However, they all have one thing in common: ultrasonic sound waves are transmitted through the fluid and detected by a sensor/transmitter, with the path the ultrasonic sound waves take varying from meter to meter. Ultrasonic flowmeters come as both flanged/intrusive meters and as clamp-on variants for non-intrusive flow measurement. They can be used to measure both gas and liquids and can measure two-phase flows, but their performance is much better when measuring a single-phase fluid. Certain mixtures or slurries can block the ultrasonic signals, resulting in poor performance, so this must be considered during flow meter selection.
Advantages of USMs
- They are robust as they have no moving parts, reducing maintenance costs associated with the meter.
- They cause little to no pressure loss, as they have no parts which obstruct the flow.
- They are available with a variety of different outputs, both digital and analog, depending on the manufacturer.
- They have high accuracy when they are installed correctly. Clamp-on variants are less accurate but advancements in the technology are resulting in increasingly more accurate devices.
- They can be used for bi-directional flow measurement.
Disadvantages of USMs
- They have a relatively high upfront cost, potentially making them more expensive than other suitable flow meter technologies.
- They have limitations in the fluids they can accurately measure. Heavily contaminated fluids and slurry flows can result in the ultrasonic waves being unable to pass though the fluid, rendering the meter incapable of accurately measuring the flow.
- Where two-phase flow such as liquid and gas is present, the performance and accuracy of the device can be poor.
Operating principles of ultrasonic flowmeters
Doppler-type ultrasonic flowmeters rely on the Doppler effect. This effect is based on the augmentation in ultrasonic sound waves coming from moving objects to the transmitter/receiver. USMs that reply on the Doppler effect for operation contain an emitting transducer which produces the ultrasonic sound wave and a receiving transducer (receiver). These meters use reflected ultrasonic sound to measure the fluid velocity. By measuring the frequency shift between the ultrasonic frequency source, the receiver and the fluid carrier, the relative flow can be calculated by the meter’s signal processing. The resulting frequency shift is named the Doppler effect.
Time-of-flight or transit time-based ultrasonic meters operate in a slightly different way from Doppler effect meters. These rely on the time taken for the ultrasonic sound wave to travel through the fluid via the transmitter and receiver — there is a difference in time from when an ultrasonic signal is transmitted from the first transducer and traverses the pipe and is received by the second transducer. A comparison is made of upstream and downstream measurements. During a no-flow state, the transit time will be the same in both directions. When flow is present, the signals move faster when traveling in the flow direction and slower if moving against it. The differences in transit time can then be used to calculate the flow rate by the meter’s signal processing.
Uncertainty
All measurement devices have a basic measurement uncertainty, but the overall effect is highly dependent on the design of the USM and path location geometry. Uncertainty can range from less than ± 0.25 % (k=2) for Class 1 devices up to ± 5 % (k=2) for clamp-on or flare meters.
Calibration
Before a meter is installed inline it is usually calibrated by an accredited flow calibration laboratory, which will have its own level of uncertainty for all calibrations performed. For example, the primary standard for oil flow measurement used at TÜV SÜD National Engineering Laboratory is a gravimetric system with an uncertainty of ± 0.03 % (k=2) for mass and volume.
Process conditions
Calibrations are generally conducted at relatively low pressures and temperatures, but these may not accurately replicate industrial applications, leading to increased uncertainty in measurement. For example, changes in temperature or pressure can alter the geometry of a USM — a key part in the velocity calculation.
International standards give guidance on this problem with detailed calculations on how to correct for temperature and pressure effects on the meter caused by changes in operating conditions from the meter calibration.
Reynolds number effects
Reynolds number effects can also impact the performance of a USM through variations in the velocity profile of the fluid. At low Reynolds numbers, the profile is parabolic or peaked in nature, while at very high Reynolds numbers the profile becomes almost completely flat.
Typically, Reynolds-based profile factor corrections are used to remove error and to linearize the meter’s performance. If physical properties change during the operation of the meter, resulting in a Reynolds number change, then this correction method will allow the meter to operate correctly — provided the calibration range covers the new Reynolds numbers.
Installation effects
Ideally, a USM should be used in fully developed, undisturbed flow, with a large length of straight pipe upstream of the meter, as they are known to be sensitive to a variety of installation effects. Single-path meters are most susceptible to installation effects, whereas dual-path and multipath flow meters exhibit less sensitivity.
However, in many applications ideal conditions cannot be realized due to space and cost constraints, with pipe work fixtures, such as bends and valves, leading to disturbances within the flow. Such disturbances can cause both asymmetry and swirl in the flow profile, which can give rise to significant errors. One solution is to use a flow conditioner upstream of the flow meter, when ideal installation conditions cannot be met.
Contaminants
USMs are single phase devices and as such are always recommended to be used in single-phase flow only. However, this may not be applicable in all situations due to flashing, liquid drop out, waxing and other fouling issues. When a second phase is present it is not only its volume or void fraction that causes measurement issues but the distribution within the pipe.
At higher velocities, the second phase is likely to be dispersed across the entire cross section of the pipe which will act to scatter and reflect the ultrasonic signal. Poor quality or even no signals will be received, resulting in a large, negative measurement error. However, at lower velocities, stratification may occur where both components separate under gravity. In the case of a liquid continuous stream, gas will stratify to the top of the pipe. In this example the lower paths of a USM will operate as intended but the higher ones (the ones in the gas section) will typically fail.
Another issue with contaminants is the filling of transducer recesses with fouling deposits. This can have the effect of bending the angle of incidence of the ultrasonic wave, or even stopping it completely. In liquid flows, wax is a common problem that can form in these locations where there is stagnation of the flow. With gases, oils are more common, but in general anything depositing in the transducer recesses will affect the acoustic signal.
Improving operation
The effect of process conditions can be successfully minimized if the meters are operated correctly. This begins with proper meter specification and calibration through to installation and maintenance. It is therefore vitally important to follow best practice guidelines and procedures to ensure USMs operate at an optimum level.
With the recent advances in secondary diagnostics, extra confidence can be given to USM measurements, as by using data analysis and trending tools, a meter can perform its own “health check” in operation. This leads to improved efficiency and potentially increased intervals between recalibrations. The diagnostics can also offer tools to identify specific process issues, which can be extremely beneficial. Using USMs in this fashion, combined with consideration of the initial installation, will ensure your meter will operate successfully for years to come.
Harry Clark is a facility lead at TÜV SÜD National Engineering Laboratory, a world-class provider of technical consultancy, research, testing and program management services. Part of the TÜV SÜD Group, it is also a global center of excellence for flow measurement and fluid flow systems and is the UK’s Designated Institute for Flow Measurement.
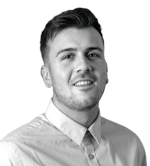
Harry Clark | Facility Lead
Harry Clark is a facility lead at TÜV SÜD National Engineering Laboratory, a world-class provider of technical consultancy, research, testing and program management services. Part of the TÜV SÜD Group, it is also a global center of excellence for flow measurement and fluid flow systems and is the U.K.’s Designated Institute for Flow Measurement.