How to keep regulators in peak working condition
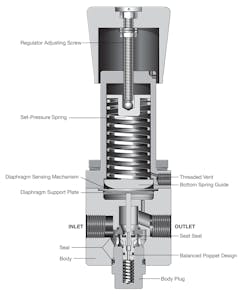
Industrial fluid systems must have specific pressure settings, flows and fluid temperatures to operate properly. Successfully maintaining these conditions requires the use of pressure regulators as key components. When one of those regulating devices malfunctions or fails outright, major problems like downstream drops in pressure can occur, compromising the quality or safety of a process.
While many factors may cause pressure variations, several common issues can be attributed to poorly operating or failing regulators. To avoid significant system downtime or costly repairs, it is important to train your technicians to troubleshoot these common issues so they can be identified and resolved. Following the three-step process below will alert you to issues before they become significant enough to harm the entire system.
Step 1: Know your specific process needs
To begin troubleshooting, it is crucial to figure out precisely what your process requirements are. That means understanding what your system flows, pressures, temperatures, process sensitivity and system media should be. Variations from the mean will be the first sign that something is wrong with your regulator. It may also indicate you have the wrong regulator installed.
Typically, the necessary component is either a pressure-reducing regulator or a back-pressure regulator. A pressure-reducing regulator should be used if you are controlling pressure from a source before it arrives at the main process. A back-pressure regulator should be used if you need to control upstream pressure. Installing one when you need the other will cause problems throughout the system.
Using the wrong regulator is an error frequently made at the installation stage of the system and can prevent the system from operating at peak performance. Such a mistake can lead to creep (a rise in outlet pressure when there is no flow caused by contamination on the seat) or the supply pressure effect (SPE). Consult with your supplier if you are unsure which regulator to install. If the proper regulator is in place, then it is time to see what else may be amiss.
Step 2: Identify the issue
Once the proper regulator has been installed, it is time to identify specifically what problem your regulator may be causing. Is the pressure dropping below your set pressure downstream or is it rising beyond your set pressure upstream? Answering this question can help you identify the root of the problem.
When pressure rises beyond your set pressure upstream, it generally indicates one of two potential issues. First, it could be creep, which may happen after initial commissioning. At that time, installation debris is still flowing through the system and may inadvertently damage the regulator by causing a small gap between the regulator’s seat and poppet. When this occurs, system media may flow across the seat and cause pressures to increase downstream.
Rising downstream pressure can cause additional problems if the pressure ratings on other components cannot accommodate the pressures creeping across the seat. The damage this may cause is avoidable if the regulator is installed properly and contains upstream filtration. You should also consider keeping a spares kit with new regulators on hand.
Unwanted pressure increases may also be caused by SPE, with the outlet pressure potentially fluctuating depending on how much pressure is in the supply line at any given time. Outlet pressures may rise if the inlet pressures drop precipitously. If your pressure increases are caused by SPE, it is time to move directly to Step 3.
On the other hand, if the pressure decreases below the set pressure, it is likely that your regulator is not the right size for the application. For example, if flow increases and the regulator does not activate to compensate, pressure will likely drop below the set pressure, also known as droop. Tools exist to help diagnose whether your regulator is properly sized for the application for which you are using it. Flow curve generators may determine that the regulator you have installed may not meet the real-world requirements of your system. If an undersized regulator is the problem, then it is time to move on to Step 3.
If none of these issues is the obvious cause of your regulator problems, it may be something less common and more difficult to diagnose. Your supplier should be able to help do a deeper examination to see what the problem may be. It is possible the regulator’s diaphragm has been damaged. This often takes the form of distortion or cracking. The reasons for distortion may vary, but it is frequently caused by excessive downstream pressure. In such cases, the distorted diaphragm may lose contact with the poppet and will not be able to actuate it. This restricts the flow of the industrial fluid to zero.
Additionally, chemical wear or cycle fatigue from pulses may also result in a cracked diaphragm or even a hole developing. In such instances, the regulator’s ability to control the amount of pressure in the system will be compromised. Reliable suppliers will be able to assess whether a diaphragm should be replaced, as well as offer advice on how to prevent the same problem from happening in the future.
Step 3. Investigate alternatives
When SPE is identified as the cause of your pressure changes, it may be time to consider installing an option that will better control it. For example, a regulator that uses a balanced poppet design can significantly reduce the area on which inlet pressure can act. In addition, using a two-stage pressure-reduction strategy will reduce supply pressure in most conditions. To achieve two-stage pressure reduction, it is necessary to install two single-stage regulators in series or combine them into a single assembly.
On the other hand, undersized regulators can be replaced with regulators with a larger flow coefficient. This will lower the possibility of an unwanted outlet pressure drop. It is also possible that a shift from a spring-loaded regulator to a dome-loaded regulator may be in order because dome-loaded regulators resist sudden flow changes more effectively. In such cases, they can keep the fluid at the set pressure, even if there are flow variations in the application.
Why regulator troubleshooting matters
Of course, the issues discussed above are not an exhaustive list of the situations that can cause poor regulator performance, though they are the most common. Sometimes filters can get clogged, and that may be fixed with a simple cleaning or replacement of the filter in question.
Working with a reliable supplier is essential to making sure you choose the right regulators to keep your industrial fluid system running smoothly. Consult with your supplier to stay up to date on the latest technology and to make sure your fluid system regulators are optimized. With this help, you will be able to keep your system operating at peak performance for many years to come.
Shaji Arumpanayil is senior product manager for Swagelok Company.
Editor's note: An original version of this article appeared on the Swagelok Reference Point blog here:www.swagelok.com/en/blog/troubleshoot-common-regulator-problems.Shaji Arumpanayil | Product Manager for Swagelok Company
Shaji Arumpanayil is a Product Manager for Swagelok Company.