Real-world illustrations of how instrumentation diagnostics improve operations
In this fifth and final installment of this series on advanced diagnostics, we will examine how companies are putting the techniques discussed so far to work and show what benefits they are realizing. As a quick review of the previous installments:
- In the first, we provided an overview of instrumentation diagnostics, with five ways they are used in process manufacturing environments.
- In the second, we focused on device diagnostics and what an instrument can tell us about its own condition.
- In the third, we took a deep dive into process diagnostics and the problems they can detect.
- In the fourth, we examined how diagnostics can identify wiring and networking problems.
Now we will look at several real-world examples of how diagnostics have made significant improvements in many different contexts, from individual instruments to plant-wide implementations. We will begin with simpler uses, and then move on to more complex examples.
Chocolate coated flowmeters
While candy making suggests small-scale production with painstaking hand work, there is enormous demand globally for chocolate variations, flavors and ingredients. Like most food and beverage applications, flowmeters are a critical element, including Coriolis mass flow technology for key ingredients.
Working with chocolate and caramel presents challenges as they can thicken quickly if they stop moving and cool in the piping, clogging everything (Figure 1). This reality makes it necessary for producers to conduct frequent calibration checks throughout all their systems to make sure equipment is not suffering from restrictions in lines caused by accumulations of hardened product.
The producer in this case is a major international confectionary manufacturer, and it uses Coriolis mass flowmeters from Micro Motion and another supplier. As is common for food production equipment, the flowmeters mount in process piping using tri-clamp mounts, so they are designed for removal and cleaning as necessary with minimal difficulty. Both suppliers in this case provided an in-situ verification system, but they did not operate with equal effectiveness. The problem was that the two metering systems provided significantly different measurements under the same conditions. According to the respective diagnostic systems, both were supposed to be correct, but given the specific working conditions, this was simply not possible.
Operators determined that a discrepancy of 15 pounds of caramel per minute suggested one of the flowmeters was plugging, even though the respective diagnostics suggested both were working. Taking the equipment apart and performing forensic analysis in the instrument shop showed that the Micro Motion flowmeters were indeed correct as indicated by Emerson’s Smart Meter Verification software, although the others were incorrect. That is not to say Micro Motion flowmeters never experienced clogging, but the verification diagnostics clearly pointed out where this was the case.
Once cleaned and reinstalled, the Micro Motion sensors and meters were tested to the reference meter. Smart Meter Verification diagnostics confirmed accurate flow measurements. Emerson engineers also recommended that the sensor be insulated to minimize product cooling and solidification, thereby minimizing plugging in the future. Plant operators implemented this measure, and since then, their Micro Motion flowmeters have delivered unquestioned measurement confidence, minimum downtime and continued operations.
Slurry-induced flow noise
A major chemical company was using legacy magnetic flowmeters on its molecular sieve water removal lines. The process at this point had 5-10% polymer solids content, which resulted in a noisy flow signal. Instrument technicians logged at least three trouble calls per year for each of the four magmeters. Each time operations complained of an erratic flow rate, technicians did not find any instrument problems.
For each of the twelve work orders per year, this company estimated it spent $6,000 from the maintenance budget to try to locate the erratic flow rate source. Due to the noisy flow signal and the inability of the installed magmeters to filter the noise, operators had to dampen the output to get a stable signal. This resulted in delayed response time, put the process at risk for reduced quality and could have damaged downstream equipment. Since the amount of slurry feed is critical to their process, operators were required to perform visual inspections on the reactors to ensure product quality for every batch.
Emerson engineers recommended replacing the existing flowmeters with Emerson magnetic flowmeter sensors and Rosemount 8732 transmitters with the DA1 High-Process Noise Diagnostic option (Figure 2). Now operators can verify the noise levels within the process, allowing for quick and easy troubleshooting. The diagnostic can be run from the local operator interface or Emerson AMS Suite.
Based on data from the diagnostic, technicians were able to adjust the sensor’s coil drive frequency to optimize the signal-to-noise ratio, thereby reducing output variability without requiring damping. All this was done externally without a process shutdown. With more stable output, operators gained tighter control of the slurry feed and eliminated the need for visual inspections.
With the diagnostic information provided by the Rosemount 8732 transmitter, operators knew their magmeters were working as intended, and they have eliminated this unnecessary action from their yearly maintenance procedures.
Detecting pipeline disturbances
Fluid turbulence is challenging for flowmeters of all kinds. Ultrasonic flowmeters can tolerate it better than many types, but to ensure the level of accuracy necessary for custody transfer protocols, natural gas pipeline measuring points use perforated flow-straightening disks to stabilize flow after passing through valves and elbows. While we imagine natural gas is a clean product, pipeline operators find all sorts of interesting debris, carried by the gas until it encounters one of these disks at a custody transfer point. So how is a flowmeter capable of detecting that a chunk of flotsam has lodged at a flow straightening disk upstream?
Emerson’s Rosemount 3418 Eight-Path Gas Ultrasonic Flowmeters measure at multiple points across the interior cross section. Consequently, they can compare flow disruptions at each of the measuring chords (Figure 3). With an eight-pair meter, that means four slices across the pipe’s cross section. Where one is disrupted more than the rest, it suggests some localized cause may be responsible, capable of affecting overall accuracy of the measurement. Diagnostics, reporting via Emerson’s MeterLink software, report when a change has been realized. If it is over a specified threshold, it will create an alarm and log when the change occurred. Operators can determine how and when to respond.
Any flowmeter in custody transfer service requires frequent verification and calibration. In many respects, the administrative side of flow measurement is as important as the measurement itself. No matter how precisely a flowmeter is calibrated in the factory, conditions in its actual installation will call for it to be calibrated again once it is fully installed, and all the relevant supporting information must be recorded. If there are performance anomalies, they must be investigated and solved.
These realities place two main demands on operators: first, the flowmeter accuracy must be beyond question; and second, all the supporting documentation must be scrupulously maintained. Today’s ultrasonic flowmeters, with their sophisticated diagnostic capabilities working in conjunction with support platforms such as Smart Meter Verification and MeterLink, can deliver these requirements on a daily basis.
Keeping the refinery running
The MOL Group and its oil refinery in Budapest, Hungary (Figure 4), have proven that building reliability and maintenance programs on instrumentation diagnostics can happen in any facility where there is a will to succeed. These efforts have placed it in the top ten most profitable refinery operations in Europe. Moreover, plant availability has been very high, maintenance costs are well below average and process safety has been exceptional.
The MOL Danube Refinery has 58 operating units using a mix of automation platforms from at least three main suppliers with a combined 40,000 tags, most of which are HART-enabled. Some units have HART I/O, but most use multiplexers to gather diagnostic data. About 5,000 tags are identified as critical. With this mixed bag of instruments, the refinery had no particular technical advantage supporting its success. Instead, the company’s positive attitude made the program work.
The head of MOL’s automation and electrical department described how the company quickly realized a range of key cost and performance benefits (Figure 5) early on from utilizing the diagnostic capabilities built into the devices.
Benefits realized are now part of everyday operations:
- Diagnostic information gained early as a problem is still developing makes it easier to reduce failures.
- Deeper insights into the technical condition of equipment, such as control valve diagnostics, supports efficient maintenance.
- Prevention of emergency shutdowns maintains production.
- A systemized framework for arranging daily work helps staff manage personnel effectively.
- Continuous learning for operators and technicians encourages personal development and professionalism.
Diagnostic advances
The diagnostic capabilities built into Emerson’s advanced instruments and valve controllers are improving constantly. The technologies are available to any company that wants to use them. For MOL, and many other successful companies, diagnostic implementation requires a change of mindset as much as anything technical. Operations, reliability and maintenance teams must recognize that by working together, it is much easier to keep a facility running continuously with stable, safe and profitable production. Emerson has worked with many companies to launch exactly the kinds of programs described here, creating more predictive and less reactive operations.
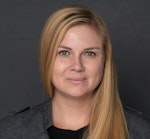
Kelly Albano | Product manager for Emerson Coriolis transmitters and software at Emerson
Kelly Albano has been with Emerson for over 12 years and is a product manager for Emerson Coriolis transmitters and software. She is focused on improving user experiences and guiding users through digital transformations. Albano holds an undergraduate degree in Environmental Engineering from University of Colorado at Boulder, and an MBA with a Marketing Management Certificate from Colorado State University.