Improving the sustainability of steam production
Steam distribution systems are part-and-parcel of process manufacturing because steam is a very versatile means to deliver carefully controlled heat energy in a variety of ways, usually via a heat exchanger. It could be shell-and-tube, plate, jacketed reactor or other configurations, but the purpose of all these heat exchangers is to raise the temperature of a process fluid, either liquid or gas.
Using steam for such purposes avoids the need for numerous small combustion or electric heaters attached to all those heat exchangers. Using steam allows the fire, or other heat source, to generate steam in a central location away from explosive environments, and then distribute it wherever it is needed. Some of the largest applications, such as a main distillation column, may be supported by their own heat source, such as a fired heater, but many smaller installations are supplied by the steam distribution system.
That said, generating steam is very expensive, and is generally one of the highest-cost utilities in a facility. The fuel burned also creates greenhouse gases, so there is a double incentive to make the operation as efficient as possible.
Heat exchangers in a petrochemical plant
If a heat exchanger (Figure 1) is sized correctly, the flow rate and temperature change of the process fluid will be matched by a corresponding flow of saturated steam, also balancing temperature and flow, so that the steam condenses as it transfers heat to the process fluid.
Saturated steam is normally used for heat exchangers, and once it transfers its latent heat to the process, it condenses back to water. If the heat exchanger is sized correctly and flows are correct, live steam should not normally exit the heat exchanger.
Once steam has condensed, it must be removed from the steam piping. Normally, it is returned to the boiler via a condensate-return system, and then added to the boiler feedwater. Separating condensate from live steam is the job of steam traps (Figure 2). How well steam traps perform affects the efficiency and sustainability of an entire steam distribution system. Steam trap service is harsh, so eventually steam traps often fail. Therefore, they must be checked frequently to ensure correct operation.
Studies suggest that normal life expectancy for a steam trap is four to eight years, depending on the application, so in a large-scale process plant, it is common to have 25% of all installed units fail in a given year. A large-scale chemical manufacturer can have several thousand steam traps, so if steam trap maintenance is not kept up to date, the negative effects can be huge.
Steam traps behaving badly
Steam traps are placed strategically throughout steam distribution systems. They may be associated with a specific heat exchanger or other piece of equipment, or they may be at a low point in the piping where condensate tends to accumulate due to gravity. Whatever the case, steam traps should release water without losing live steam. They must open to downstream pressure, while maintaining steam-line pressure.
Steam system designs assume all traps are functioning normally all the time, but they malfunction in two ways (Figure 3).
First, some do not seal completely or can fail open, allowing condensate to sputter out, while also releasing live steam. A U.S. Department of Energy survey found that 5% to 20% of steam traps fail annually, with the steam lost through open traps equal to 33% to 50% of line capacity, which is very costly. Injecting live steam into a closed condensate capture system can be a problem if it cannot handle the pressure. Pressurizing the outlet side of a steam trap can cause it to malfunction and not release condensate as it should, multiplying the effect to all the steam traps connected to the header
Second, the opposite can also happen where some steam traps get stuck closed. Condensate then accumulates and backs up into the steam line (Figure 3). If it is attached to a heat exchanger, eventually it will fill with condensate and block steam flow, which can lead to heat exchanger stalls. Slugs in the steam pipes can also cause water hammer, leading to pipe corrosion, erosion and cracks.
Effects on sustainability
The two conditions just mentioned both affect sustainability adversely, but in different ways.
Steam loss, due to a failed-open steam trap, is a link in a direct energy loss chain. The boiler must work harder to make up for the loss, so it consumes more fuel and creates more emissions, since most boilers burn either oil or natural gas. Leaking steam can also lead to a shortage and system pressure sag, requiring additional boilers, leading to even more emissions. Discussions of steam leaks from steam traps and elsewhere in the system usually point to the alarming costs of additional fuel required, along with the growing carbon footprint to make up for the losses.
The problems caused by failed-closed steam traps are more subtle. Discussions around this topic tend to emphasize hazards caused by slugs of water shooting through the steam system and causing damage to equipment.
At the same time, if the steam trap supporting a heat exchanger is stuck closed, either due to malfunction or over-pressurization of the condensate recovery system, steam cannot flow through the heat exchanger in sufficient amounts to deliver the heating step that the process needs. Perhaps some steam is flowing, but condensate backed into the heat exchanger reduces the working exchange surface area. Whatever the situation, the process fluid is not being heated sufficiently. Operators observing the effect in the control room may assume it is caused by fouling (Figure 4) because the results are similar.
Each issue invariably reduces product quality, adds cost and increases carbon footprint. Maintenance may even call for a shutdown to check the heat exchanger for fouling when the actual cause is much simpler and easier to fix without a shutdown.
Problems can be addressed quickly since steam traps are simple to service, and new units are not expensive. Some plants perform monitoring manually, sending technicians on rounds to figure out which units seem to be performing correctly. Technicians often carry a thermal imaging device to verify the correct temperature profile, or a portable audio sensor to capture characteristic sounds. These approaches can be very effective, but they require a human technician with sufficient training to interpret the results.
But given personnel constraints at process plants these days, how often can an inspection happen to a given steam trap? Given general performance statistics, inspections several times per year for each steam trap are a practical impossibility in most plant environments.
Automated, continuous monitoring
To solve manual monitoring problems, acoustic sensors can be mounted permanently on the piping adjacent to a steam trap (Figure 5), able to sense to its operation continuously. Such sensors are internally powered and use WirelessHART networks to send data to maintenance and reliability departments for analysis. These devices can be mounted with hose clamps with no penetrations, so there is no need for a shutdown.
Since it is not practical to monitor every steam trap, maintenance and reliability teams should identify the most critical points, along with the bad actors. Critical steam traps typically include those used in high-pressure and high-quality steam systems, and those associated with highly sensitive equipment. These are normally first to be outfitted with acoustic monitors. Once savings from improved performance begin to accumulate, new possibilities emerge. Investment in additional sensors quickly pays for itself.
Data collection and analysis software tracks individual steam traps and presents a picture of performance in real time via preconfigured dashboards (Figure 6). Technicians can see which steam traps are working correctly, and which are in a failure mode. The software estimates lost energy and resulting costs, including the effect on carbon footprint. Maintenance can plan activities appropriately, dealing with small problems before they become serious issues.
Naturally, the data may need some interpretation. A steam trap reported as inoperative may result because the equipment only operates intermittently and may simply be shut off. On the other hand, a steam trap attached to a process that runs continuously, or at least regularly, should develop characteristic discharge patterns. If these indicators change, such as a sudden increase in condensate volume, there is probably some other cause.
Basic operation versus system improvement
Malfunctioning steam traps can make a steam system less efficient, but even when operating correctly, they cannot improve on it. Most steam distribution systems are under-instrumented, so it is difficult to determine where energy is being lost, either simply through leaks, heat dissipation in the piping or where specific applications are consuming more steam than is necessary.
If a facility is serious about sustainability, moving beyond steam trap performance monitoring is the next step. Maintaining high-quality steam throughout a distribution system requires additional attention, which is difficult without proper measurement. Maintaining steam delivery within a facility without losses from leaks is a major challenge, particularly with aging infrastructure. Measuring steam system temperature, pressure and flow rates at strategic points delivers insights into plant performance, and technicians can use this information to perform adjustments and pinpoint issues.
Recent improvements in flow metering technologies (Figure 6) deliver reliable information, even in the most challenging installations. Tying flow and other variable measurements into supervisory software delivers valuable, concise information to simplify steam system operations.
Making a facility more sustainable requires paying attention to a wider range of operating parameters than may have been the case previously. Small energy losses might have been tolerated in years past, rationalizing the situation by saying, “It is not worth fixing.” Such situations are becoming more difficult to ignore because there is a cost when doing nothing that can escalate quickly, and steam traps and steam systems are a prime example. Adding monitoring capabilities is a critical first step, but they only identify that a problem exists. Solving the problem means acting on the information by fixing steam traps and related systems before they contribute further to ongoing waste. That is the path to sustainability.
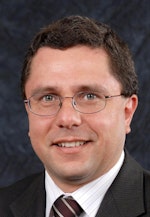
Marcio Donnangelo
Marcio Donnangelo is a global business development manager with Emerson’s Automation Solutions business in Houston, Texas, specializing in wireless technologies. He is an industrial electrical engineer with 25 years of field experience applying industrial automation solutions for customers across multiple business segments and industries including refining, petrochemical, chemical, pulp and paper and others.