Wireless remote monitoring systems answer the call
Lower oil prices, high exploration costs and environmental compliance prompt the oil and gas industry to take a more aggressive approach in implementing automation to optimize processes for more significant gains in productivity, cost-efficiency and emissions containment. In the past, workers traveled throughout the oil field to manually monitor metrics of operations such as tank levels, oil flow and valve position. Automation and connectivity provide oil and gas companies with opportunities to implement smarter solutions in oil field and process management. Global research analyst IDC Energy Insights predicts that the top 50 oil and gas companies will double investments in oil field operation automation to double the productivity of operations by 2020, reported Rigzone.1
As the oil and gas industry moves to automated controls, wireless monitoring and control systems provide the capability to automatically track, manage and connect different and remote assets to improve operations and reduce costs. These wireless sensor control systems can help workers stay informed on the real-time status of flowmeters and pumps, wellhead casing and tubing pressures, tank levels, emissions and more for better equipment utilization and to satisfy environmental regulations.
More than just automating data collection, these remote telemetry systems are configurable to shut down operations or alert operators when parameters meet programmed thresholds. Historical data can provide insights into trends for better asset management such as ensuring that storage tanks never overflow or that pumps operate at optimal levels.
With a wireless remote monitoring and control system, workers can remotely track conditions, troubleshoot problems, change monitoring parameters and stop specific operations from the convenience of a remote computer. For example, in upstream exploration, companies must manage and dispose of water produced from wells. One disposal method is dispatching trucks to empty storage tanks. By monitoring flow rates for each well along with storage tank capacities, an operator can anticipate when to schedule trucking companies responsible for emptying tanks.
Wired versus wireless
While the oil and gas industry predominantly uses wired systems that connect sensors to a data collection system, wireless remote monitoring systems prove most cost-effective and versatile for use in existing installations in the hostile and hard-to-reach locations of oil fields. For new installations, wireless sensors and telemetry provide for the deployment of the necessary automation to start producing sooner.
The use of remote wireless telemetry for monitoring flowmeters offers these significant advantages over their wired counterparts:
- The electrician does not need to run power, wires or conduit, simplifying installation and meter configuration.
- The absence of wiring requirements reduces costs.
- An operator can easily repurpose a meter to a new process without worrying about how to get the signals back to the control system.
- With ever-changing communication protocols, operators can upgrade every device on the system to HART, Modbus or other protocol by swapping out the Gateway instead of each device.
Look Mom — No wires
A significant advantage of using a wireless system is that it requires no wires. A wired system needs cabling to connect different endpoints. In addition to trenching expenses, cabling can cost $10 to $20 per foot. Depending on the wired system’s location, costs for running conduit over large areas can make a wired network too cost-prohibitive. Should a wired monitoring system require repair or reconfiguration, new cabling and trenching is needed to complete the job.
Wireless remote monitoring and control systems simulate the architecture of a wired system using links instead of cabling to transmit data. For example, in a tank level monitoring application, common in the oil and gas industry, radio nodes would power and receive data from level sensors located on the tank without the need for wires or power lines (see Figure 1). Nodes transmit data to a gateway that formats it for accessibility by a programmable logic controller (PLC) in a control center or through an internet connection (see Figure 2).
Figure 2. Shown is a schematic of the configuration of a wireless remote monitoring and control system. Radio nodes wirelessly transmit data collected from sensors to a gateway that formats information for accessibility by a PLC in a control center or internet connection through a laptop. With gateways able to accommodate up to 10,000 nodes, a wireless sensor control network can cover a geographic range of hundreds of square miles.
A wireless system can cost a few hundred to a few thousand dollars per measured point. However, they are still cost-competitive compared to wired systems, which have expensive installation requirements. Plus, technicians can configure and test wireless systems — along with their sensors — in controlled environments, reducing on-site work by 50 to 70 percent.
Operate in different terrains and environments
Most oil and gas fields include many miles of rugged terrain and harsh environments that make it difficult and often dangerous to access by workers. Properly specified wireless remote monitoring and control systems operate under hostile conditions, in rough territories as well as over roads, waterways, buildings or other structures that often limit wired connectivity.
In some scenarios, wired systems are uninstallable on property not owned by the operator. The radio nodes of a wireless remote sensing system sustain robust data transmissions in unlicensed industrial, scientific and medical (ISM) bands through different terrain, structures and weather, and they continue to operate for years without being affected by weather elements. Only a wireless remote monitoring and control system certified for operation in hazardous areas should work around caustic or explosive environments.
Because sensors and other components are not physically connected, wireless systems can withstand lightning strikes that destroy wired systems. If lightning hits a sensor in a wired system, the effects propagate along the cable, often destroying equipment attached to it. Wireless networks can better withstand rapid changes in electrical fields when lightning strikes. While nothing survives a direct hit, a struck wireless system typically only loses one asset as opposed to the entire network.
Accepts multiple and varied sensors
When monitoring various parameters in the same network, a wired system requires that each sensor is wired to the controller and connected to an interface port. Larger networks could need a wired system to have a sizable interface panel with different interface types. A wireless system provides for a digital communications interface (4-20mA, Modbus RS485, HART) that allows multiple sensors to connect to the controller over a single port without the expense of running conduit. An Ethernet interface module can tie information from the Gateway into a local Wi-Fi network for local access or a modem that connects the internet and a cloud service provider.
In addition, a versatile wireless monitoring and control system is sensor agnostic. This allows users to build an entirely wireless network using the best sensor selection of their choice. Some applications involve monitoring various parameters (pressure, level, temperature and flow) of different assets. Others require specific sensors to address the conditions of the application. For example, the material flowing through the system often dictates the best flow measurement technology (see Figure 3).
Figure 3. Shown is a set of wireless flow totalizers connected to turbine flowmeters to monitor water and oil flow rates within pipelines. In this upstream oil and gas application, two units on the left count water rate while those on the right count oil. The flow totalizers show field displays of flow rates and totals, providing continuous real-time information instead of snapshot views. Data and diagnostics are available locally using the display of the battery-powered flow totalizer as well as remotely from a gateway using Modbus standard protocol.
Wireless connectivity solves the issue of mixing multiple sensor interface types by allowing sensor interfaces to coexist within the same network and supplying nodes with different sensor interfaces. Operators can quickly add or subtract sensors as needed to measure various parameters. The network brings data from different sensors to a single point with a single data interface.
Because sensors represent significant power usage, wireless systems can help reduce energy costs by putting sensors into sleep mode by either turning them off or placing the entire wireless telemetry system into a low power state and "waking up" on a schedule or when triggered by an event.
Large scalability
In oil fields, communications distance can be significant. The area between monitored assets can range from 20 to 50 yards or extend to more than 1,000 yards. Robust gateways within a wireless remote monitoring system can accommodate hundreds of transceiver nodes, enabling the network to cover a geographic range of hundreds of square miles to meet long-distance communications among widely dispersed assets.
Before choosing a wireless remote monitoring and control system, ensure it meets all operating requirements. Many off-the-shelf wireless solutions cannot operate in hazardous environments. Some manufacturers require specific sensors. While cost is a factor, it is only one component of choosing a wireless sensor control system that can address an operation’s needs now and in the future.
Reference
Sandro Esposito is sales and marketing director for SignalFire Wireless Telemetry. He can be reached at [email protected]. Visit signal-fire.com for more information.
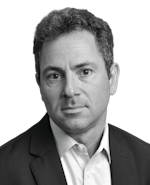
Sandro Esposito | Vice President of Sales & Marketing for SignalFire Telemetry Inc.
Sandro Esposito serves as Vice President of Sales & Marketing for SignalFire Telemetry Inc, with responsibilities for managing the portfolio and commercialization of the company’s wireless telemetry solutions. In addition to possessing more than 24 years of experience in the process control and automation industry, he holds six patents and has published 12 papers related to industrial controls and smart technologies. A graduate of College Ahuntsic in Montreal, he holds a Bachelors degree in electrical and instrumentation engineering and is actively involved in the International Society of Automation.