Level transmitter technology options: How to choose
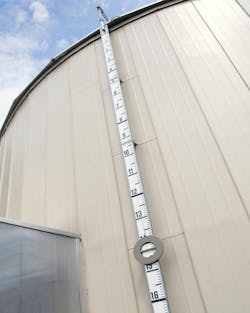
The need for reliable level measurement is not uncommon. There are countless applications that require level measurement to function properly. However, even though the need is abundant, the knowledge surrounding it is not.
There are several approaches one can take to achieve level measurement (through level transmitter technology), but they all have different pros and cons depending on the process they are earmarked for. More importantly, they all come with an associated cost. Some technology is on the expensive side, but if the level application in question does not require the features associated with said technology, a less expensive alternative can be just as effective. In fact, there are several key factors that need to be explored before settling on the appropriate level transmitter technology for a given application.
Application type, vessel design and process variation
There are three key questions to ask before beginning the decision-making process on which level transmitter technology to choose. It is important to collaborate with an expert when going through this process, but for that individual to provide you with the very best advice, you will need to gather the following information.
The first questions surround what the level application in question is. For example, what is the nature of the control of the process? Is it continuous or is there an on/off capability? The most important factor here is the repeatability of the process. Next, is the application a batch/recipe control application? If it is, then high accuracy is required. The same goes for a custody transfer application. In this case precision accuracy is paramount.
Continuing the exercise of identifying what kind of level application it is, what kind of output is needed? This could be an analog 4-20mA, Modbus or Ethernet. Finally, do we need a visual indication or verification function?
Identifying and understanding the requirements will ensure the right technology with the proper costs is selected.
The next step is to identify the vessel. The vessel type will play a part in dictating which technology is applicable for a certain requirement.
Tanks can come in different forms and have various features:
- Above grade product tank
- Below grade tank or sump
- Floating-roof storage tank
- Bullet or spherical pressurized tank
- Material of construction
- Instrument entry port size and location
Any combination of these elements will help guide your vendor in assisting you to apply the best instrument for your installation.
Finally, there are the process features to consider. The physical properties of the process will narrow the options available. A checklist of questions must be considered before making any final decisions.
Is the vessel pressurized? What is the temperature range? Is there a specific gravity or density? What is the viscosity? Is it Conductive/Dielectric Constant? Is there concern for corrosive or reactive behavior? Are there vapors or fumes in the dead space above the liquid?
Having answers to all these questions ensures that you’ll receive the very best guidance from your vendor, enabling you to make the most informed and effective selection.
Level transmitter technologies
The next question one may ask themselves is, “What are my options?” Once the decision-maker has all the relevant information applicable to their unique process, how do they make a selection? There are many different transmitter technologies available when attempting to achieve level measurement. They all have unique features and can sometimes be challenging to match up with the factors present in a certain process. What is most important is to consult with an expert before making any costly purchasing decision.
Pressure level transmitter technology comes in two distinct forms: Differential and submersible. Differential pressure can be used on pressurized above grade vessels. It is a technology that requires a stable density. Diaphragm seals associated with the differential pressure technology allows it to be ideal for dirty or viscous processes.
Submersible technology utilizes a wetted sensor and requires a small entry port at the top of the vessel or below grade sump, reservoir or lake, suspended by an electrical cable to the bottom.
Conductivity level transmitter technology is another option to explore, yet it requires the process to be a conductive media. Through this technology, a small top connection is required for the rigid or flexible probe to be easily installed. It is important to note that viscous material can be slow to respond to a falling level. However, it is good for corrosives when compatible probe materials are selected.
Guided-wave radar technology provides greater accuracy than conductivity transmitters, but the installations are very similar. Furthermore, the dielectric constant on the process must be stable. If not, either inaccurate measurement or a loss of signal is bound to occur.
Ultrasonic transmitters are the ideal choice for harsh processes, as the sensor never comes in contact with the product that is in the tank. They are also capable of long-range measurement, which is why a large number of ultrasonic transmitters are used in open tanks or sumps and reservoirs.
Radar transmitters are another option and considered to be one of the most accurate. This type of transmitter is commonly used for custody transfer applications due to the need for such precise measurements. It stands to reason that it is a very complicated installation and configuration.
The final transmitter technology type for the purposes of this discussion is the magnetostrictive variety. This utilizes a wetted sensor and float. Thus, it is not commonly used in viscous processes. What makes this technology unique is that it can give separate outputs for level, interface level and multi-temperature points in one probe and connection. It is also very accurate as we see it used frequently for custody transfer and batching. It is also a very convenient technology as through its digital “transit-time” signal processing, the operator can quite literally set it and forget it. Finally, it can be installed both internally and externally on magnetic level gauges.
It is safe to say there is much information to go through before making a decision on the level transmitter technology to choose. Each one of these technologies comes at a certain cost. Some are much more expensive than others, making the decision more impactful. It is important to avoid paying for unnecessary features that drive up the cost. Alternatively, cutting corners for cost saving purposes can be a critical mistake if the process requires more robust technology. The key is working with an expert that understands all the inputs for your specific challenge and can guide you through your decision.