The platinum resistance thermometer: Everything you need to know
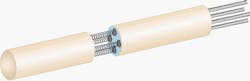
The platinum resistance thermometer — also called a PRT or Pt100 — is the most commonly used instrument to measure industrial process temperatures. Accuracy, long term stability and repeatability are the main features responsible for its popularity. The basic PRT is an electrical resistor that uses platinum wire as the load. Platinum is used because it has a very linear resistance vs. temperature relationship over a wide temperature range of -196°C to 850°C. As the temperature increases, the electrical resistance increases and does so in a very predictable manner. PRTs are used for measuring industrial processes across all industries and they are the choice for laboratory measurements used to calibrate other temperature sensors.
The two most common sensing element types are wire wound and thin film. Wire wound sensing elements are typically used for applications that require high accuracy and long-term stability. Figure 1 shows one type of wire wound sensor construction in a dual element configuration. Each coil has 50 ohms of resistance at 0°C so two coils are connected to form one sensing element that has 100 ohms of resistance at 0°C. The coiled wire is 0.0007-inch diameter platinum wire inserted into a ceramic tube of 0.063-inch diameter and sealed with glass on each end. The leads are about 0.012-inch diameter platinum alloy for added strength required for industrial processes.
The sensor is potted in a variety of housings designed to provide the best heat transfer and interface with the process whether it is gas, liquid or solid.
The thin film sensor style is constructed by depositing a thin film of platinum on a ceramic plate then using a laser, or other means, a path is trimmed to form a narrow ribbon of platinum that will have 100 ohms of resistance at 0°C. Leads are then attached and covered with glass. The result is a very small sensor around 0.020-inch thickness and 0.125-inchs square. They are also made rectangular in other sizes.
They are low cost and can be very durable if packaged correctly. Long term stability and repeatability are not quite as good as the wire wound sensor but in certain applications the added durability over wire-wound may result in a more accurate temperature measurement.
Each of the sensor types for industrial applications are constructed to meet the requirements of ASTM 1137 or IEC 60751. The standards specify an ice point (0°C) resistance and a temperature coefficient. The ice point resistance is measured in an ice bath constructed of crushed ice and water placed in an insulated container. The ice and water used are free of impurities that can affect the ice point temperature. As with everything. there is a tolerance — this one called interchangeability, associated with this measurement and the PRT standards provide guidance. Figure 3 shows the interchangeability beginning at 0°C and increases as the temperature moves away from 0°C.
The various interchangeability bands are labeled as classes or grades in the standards with grade or class A being tighter tolerance than grade or class B and so on. Table 1 shows equations that can be used to calculate the interchangeability at any desired temperature in degrees C.
Table 1: Interchangeability Tolerance Defining Equations
ASTM E1137 Grade A ± [ 0.13 + 0.0017 | t |]
ASTM E1137 Grade B ± [ 0.25 + 0.0042 | t |]
IEC 607512 Class AA ± [ 0.10 + 0.0017 | t |]
IEC 60751 Class A ± [ 0.15 + 0.002 | t |]
IEC 60751 Class B ± [0 .30 + 0.005 | t |]
IEC 607512 Class C ± [0 .60 + 0.010 | t |]
Note 1: | t | = absolute value of temperature of interest in °C
Temperature coefficient of resistance, or TCR, is the amount of resistance change per degree C of temperature change. An industrial grade PRT has a TCR of 0.00385 ohms/ohm/°C. Or in other words there is an average of 0.385 ohms of resistance per degree C of temperature change between 0°C and 100°C as defined by the standards.
In equation form:
α = (R100 – R0) ÷ (100R0)
α is the temperature coefficient
R100 is the resistance measured at 100°C
R0 is the resistance measured at 0°C
Note that at 100°C the nominal resistance reading is 138.5 ohms.
There are other coefficients such as for lab standards which use 0.003925 and a nearly obsolete US industrial grade standard of 0.003902, but 0.00385 is now the most common for industrial applications. A graph of resistance vs. temperature relationship will show minor dips and turns throughout the full range of PRTs and these are defined by the International Temperature Scale of 1990, or ITS-90, equations. That is another huge topic that I will not cover here. These are very small non-linearities and are typically not accounted for in industrial applications. A more user-friendly mathematical relationship of resistance vs. temperature to use for industrial applications is the International Practical Temperature Scale of 1968, or IPTS-68. The equation for the R vs. T relationship is called Callendar-van Dusen, or CVD, and defines the relationship between resistance and temperature with slightly less accuracy than the ITS-90 equations.
For t > 0 °C: Rt = R0 (1 + At + Bt²)
For t < 0 °C: Rt = R0 (1 + At + Bt² + C (t - 100) t³)
t = temperature in °C
Rt = resistance at temperature t
R0 = resistance at 0 °C
When specifying a PRT it is important to match the temperature coefficient and resistance at 0°C to the instrumentation input requirement. Failure to do so will cause a large measurement error. For example, if a TCR of 0.003902 and 100 ohm ice point resistance is used with an instrument that is set for a TCR of 0.00385 and 100 ohm ice point resistance, the indicated temperature at 100°C will be about 1.35°C higher than actual temperature. It will however read accurately at 0°C but as temperature moves away from 0°C in either direction the error increases.
Summary
The wire wound platinum resistance thermometer was patented in 1924 and since then has become the most used device for measuring laboratory and industrial process temperatures. High accuracy, long term stability, repeatability and integration with electronic controls are the features responsible for the popularity. A rather simple electrical resistor that when heated increases in resistance in a very predictable manner. Understanding the nuances of this relationship is necessary to achieve an accurate temperature measurement.
Bill Bergquist is principal applications engineer and RTDologist at Burns Engineering with 37 years of experience in temperature measurement with RTDs and thermocouples in the aerospace, industrial and laboratory markets.
Bill Bergquist
Bill Bergquist is a principal applications engineer and RTDologist at Burns Engineering with 37 years' experience in temperature measurement with RTDs and thermocouples in the aerospace, industrial and laboratory markets. For more information, email [email protected] or visit the Burns Engineering RTDology page on YouTube to view numerous how-to videos on temperature measurement.