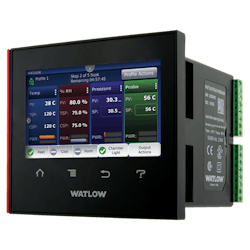
Selecting the proper process controller is not always a simple process. There are a number of different variables that should be considered before finalizing any decision on the best approach to take with a process controller.
Not every process needs to be treated the same. Even painting with a very broad brush, there are some very basic details that should be established before determining which is the best process controller to utilize. For example, what exactly is being controlled? Is it temperature regulation that is needed or are there also needs for pressure, humidity and flow? Will the controller be communicating through a network and, if so, what are the characteristics of the network the process controller is earmarked for?
These questions are just of the vary basic variety. The key is to make sure that before any costly decisions are made, there should be a consultation with an expert, so the proper controller is installed. That way, the chances for errors and a resulting inefficient process will be greatly reduced. There are many types of options to sift through, and keying in on the ones that benefit your process the most will guide you to the most appropriate controller.
Type of control
The first step in the decision-making process is to determine what you want to control and how many control loops are required. Is the plan to simply control temperature? Do you want to control pressure, humidity, level and/or flow? The type of control and number of control loops needed will directly affect the type of inputs and outputs that need to be present on a process controller. For example, if the goal is to control temperature in a process, there needs to be some type of temperature sensor input. This could be a resistance temperature detector (RTD) or a thermocouple. Other types of analog inputs may be used for pressure or flow, such as 4-20mA or 0-10V. Like most input options, this can be a “tip of the iceberg” situation, leading the decision maker down a path where there are even more variables that should be considered. Does it make more sense to use a RTD or a thermocouple for a particular process? Both have their own advantages and disadvantages that need to be considered, leading to a choice that makes the most sense.
In some cases, these inputs may just be monitored, and the data recorded. But in other cases, you will use the data to control an output. Once all the inputs are determined, then the outputs need to be defined. What do you want the process controller to drive? If you are modulating an electric heater, you would need either an SCR or relay output. If you need to modulate a valve to control process flow or heater fuels source, you might use an analog output. Each control loop will include at least one sensor input and can have a variety of outputs. This is your control philosophy, and it needs to be determined before you can choose a process controller.
Network
As technology evolves, as a user, one would hope and assume that it becomes “better.” But what does “better” mean exactly? In this case, one of the elements that makes many process controllers better than their predecessors is their compatibility. A very common control system architecture known as supervisory control and data acquisition, otherwise known as SCADA, is present in most environments that would require a process controller. However, there are several different SCADAs currently in operation. This means that for a process controller to be compatible with a specific process, it first and foremost needs to be compatible with the SCADA present. The controller needs to seamlessly interface with the equipment that requires some level of control. Fortunately, the assumption above about process controllers having improved compatibility is true. Today, more and more suppliers offer a litany of network options. However, it is a critical piece of the puzzle that should never be overlooked before making a sizable investment in a process controller.
Package and interface
Finally, after determining your control philosophy and making sure it fits your SCADA, you can choose the package that fits the applications. To best unpack the motive behind this decision, it is good to start with a simple one-or-the-other question. Is this a new process with a new controller? Or is this replacing a previous controller? Let’s start with the latter. If this is a replacement, the size may be less of a decision than a requirement. There is only so much room in a control panel, and the new process controller simply cannot exceed the size of the opening that exists. A controller must be selected that works with the setup in place.
If this is not a situation where a controller is being replaced, size is still going to be a factor, but it may not be clear at the outset what that size needs to be. Typically, the more functionality the controller needs to have, the larger it is going to be in physical size. Not only does functionality partially dictate size, but there is also another element that could most aptly be described as a convenience factor that plays a part: the size of the buttons and screen. Depending on preferences of the individuals that will be engaging with the controller on a regular basis, it may be advantageous to install a process controller that is easier to read with a larger screen and easier to interact with through larger buttons. If there are several control loops, or if there is a desire to view a considerable amount of data locally, it might be a better choice to interface the process controller to on HMI (Human Machine Interface). An HMI can be customized to the application to enhance ease of use and more easily detect possible errors in the process. In addition to preferences, the size of the screen and buttons should also be determined by the estimated use. If there are going to be relatively numerous interactions with the controller regularly, the investment into a controller that is more convenient to work with may make sense. However, if the fit is such that a larger controller is an impossibility, and you are fairly confident that ease of engagement is not something that will matter too much one way or another, then a smaller process controller is likely the best solution.
Most importantly, if someone is not an expert on process controllers, it is recommended that they consult with someone who is. There are many subtle variables that should all be accounted for before making a purchasing decision.
Jon Irvine is the sales manager, process heating, for Valin Corporation, a leading technical solutions provider for the technology, energy, life sciences, natural resources and transportation industries. Valin offers personalized order management, on-site field support, comprehensive training and applied expert engineering services utilizing automation, fluid management, precision measurement, process heating and filtration products. For more information, please visit www.valin.com.
Jon Irvine | Sales Manager, Process Heating, for Valin Corporation
Jon Irvine is the Sales Manager, Process Heating, for Valin Corporation, a leading technical solutions provider for the technology, energy, life sciences, natural resources and transportation industries. Valin offers personalized order management, on-site field support, comprehensive training and applied expert engineering services utilizing automation, fluid management, precision measurement, process heating, and filtration products. For more information, please visit www.valin.com.