Radar technology is increasingly viewed as the best method of level measurement, but this is not necessarily true for every application. Radar sensors have certainly made great advancements in performance, accuracy and even cost, but they are not a one-size-fits-all solution and should not be treated like one.
Though radar is versatile, there are some applications where ultrasonic level technology is a better fit. Approaching level measurement with a fit-for-purpose mindset instead of a blanket approach is important for safety, performance and overall product quality. Endress+Hauser's level expert, Scott Peterson, discusses the differences and benefits of ultrasonic and radar technologies and which applications ultrasonic should be considered.
What is ultrasonic level measurement?
Ultrasonic level sensors use the time of flight (ToF) principle to measure level. The ultrasonic transducer generates a mechanical sound pulse, which is directed through the air to the process. When this pulse encounters the process surface, it reflects back to the transducer. The transmitter is basically a high-tech timer, measuring the time it takes the pulse to travel to the process and back. This time is directly proportional to the distance from the gauge to the process surface.
What are the differences between ultrasonic and radar level measurement sensors?
Radar level measurement operates based on the same ToF principle as ultrasonic; however, radar uses high frequency microwaves emitted from an antenna. Rather than reflecting based on a change in density as sound waves do, microwaves reflect based on a change in impedance caused by the change from a low dielectric medium (air) and a higher dielectric constant of the process medium. Since microwaves are electromagnetic and do not require air as a transmission medium, radar is well-suited for use in a vacuum or when other gases are present in the empty space. Radar is a safe solution even under extreme process conditions including pressure, temperature and vapors.
What are the benefits and advantages of ultrasonic level measurement?
The ultrasonic method is a proven and cost-effective solution for level measurement in liquids and bulk solids. It is characterized by easy planning and assembly, fast and safe commissioning, a long service life and reduced maintenance costs. Since ultrasonic does not rely on dielectric constant for reflection, it is well suited in use where the process media has low (less than 1.5) dielectric constant, with the exception of hydrocarbons. It is also well suited for open channel flow measurement and in use with weirs or flumes.
What are some common applications where ultrasonic sensors are used and should be considered?
The main limiting factor for radar is the dielectric constant. Materials with low dielectric constants may not provide enough change in impedance to cause a reflection. This results in the microwave energy passing through it and reflecting off the vessel bottom. Some materials with dielectric constants too low for free space radar are dry sawdust, wood chips, white cement and many plastic pellets. For these applications, ultrasonic transmitters can provide a measurement where the radar transmitter would not.
Some users moved away from ultrasonic sensors because of previous challenges caused by dust buildup or condensation on the transducer’s faceplate; however, an ultrasonic sensor equipped with automatic self-cleaning, such as the Endress+Hauser Prosonic FDU91, eliminates failures caused by dust buildup.
What challenges can ultrasonic level measurement help overcome?
Ultrasonic sensors can help overcome the challenges end users might experience in tight spaces. They are ideal for installation in tight places due to the relatively small size of the sensor and the ability to mount a sensor directly to a ceiling. An ultrasonic sensor can also be helpful in cases of flooding; when used with a flooding protection tube, the sensor can ensure a high measurement is indicated even if it is under water. In outdoor installations, where temperatures can drop below freezing, ultrasonic sensors with an integral heater can prevent ice formation on the device. This would ensure reliable measurement year-round. Icing can cause issues with radar, as the ice has a high dielectric constant, which may attenuate the radar signal at or near the source. If this occurs, there will not be sufficient radar signal reaching the product surface to give a level measurement.
What ultrasonic level measurement devices does Endress+Hauser offer?
Endress+Hauser offers a broad range of devices for ultrasonic level measurement. The Endress+Hauser Prosonic product line features 12 ultrasonic, ToF sensors and two powerful transmitters. All are unaffected by dielectric constant, density and humidity. They are also unaffected by buildup of dust or condensation. The Prosonic FMU90 ultrasonic transmitter coupled with a FDU9X transducer is an excellent choice for many of these applications. The FMU90 offers additional features like totalization, data logging, differential measurement, pump control and open channel flow tables. The FMU90 is also available in a two-channel model to reduce overall hardware costs.
Scott Peterson is the national product manager at Endress+Hauser USA for level. He is responsible for the strategic direction of the level business unit including life-cycle management, technology and application identification, as well as marketing and business development for the level products. Peterson has a Bachelor of Science in electrical engineering, and he has spent more than 32 years in process instrumentation and control with industry-leading companies.
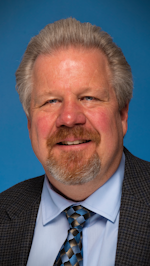
Scott Peterson | National Product Manager at Endress+Hauser USA
Scott Peterson is the national product manager at Endress+Hauser USA for level. He is responsible for the strategic direction of the level business unit including life-cycle management, technology and application identification, as well as marketing and business development for the level products. Peterson has a Bachelor of Science in electrical engineering, and he has spent more than 32 years in process instrumentation and control with industry-leading companies.